Project C 06
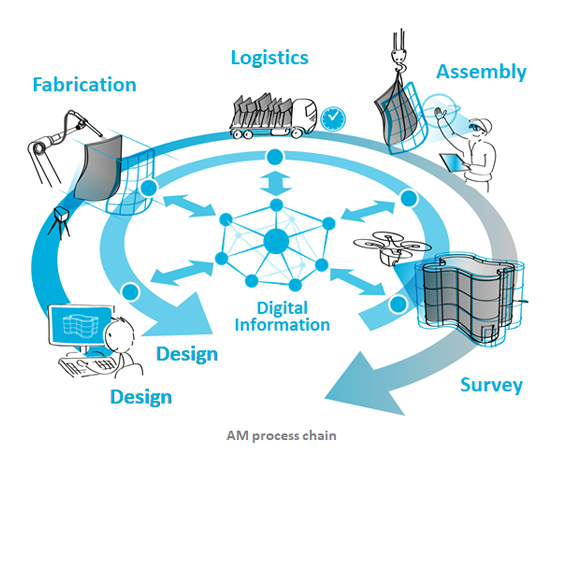
Program
Networking with other projects
Poster
TRR277_C06_Poster_1-DFG-BegutachtungTRR277_C06_Poster_2-DFG-Begutachtung
Integration of Additive Manufacturing in the Construction Process
The introduction of additive manufacturing in construction is expected to lead to fundamental changes along its entire value chain. While traditional construction processes are characterized by the fragmentation of construction knowledge, new digital tools allow the integration of all project participants already in early project phases. The prerequisite for this is a bi-directional flow of information into a central building information model. The aim of this project is to investigate the bi-directional relationship between production and planning at the scale levels of component fabrication (using computer vision and machine learning for fabrication improvement), component assembly on-site (using mixed reality besides others) and on the industry scale (e.g. integrated project delivery).
Aim
The integration of additive manufacturing into construction requires an interdisciplinary approach. The different competences of the team – digital fabrication in architecture (Hack), geodesy and photogrammetry (Gerke) and construction management (Schwerdtner) – lead to research from diverse perspectives on the various scalar levels of construction to be viewed holistically: component, building and industry scale. Our aims can be motivated as follows:
- Multiple stakeholders share and consolidate their (fragmented) knowledge into a centralized BIM model
- Holistic process understanding allows collecting data before, during and after the fabrication and assembly process on site.
- Process analysis and interpretation will form an integrated construction delivery system
- Digital tools enable continuous and uninterrupted quality control throughout the entire construction process.
- Sensor feedback: Unforeseen issues during production and construction that lead to deviations (as-built) from the design (as-planned) can be corrected instantly.
Exemplary Research Questions
- What could a future value chain with an information flow and the early involvement of construction competence look like?
- How is it possible to trace the actual assembly information (location, time, process parameters) back to the BIM (update of digital twin)?
- What kinds of construction-related information and parameters must be tracked before, during and after the AM process until each component is completed?
- How does mixed reality improve the on-site assembly of building components? Capabilities, challenges and limitations.
- Which sensors and measurement methods are most suitable for capturing the current geometry and condition of an AM-component and comparing it to tolerances?
Program
WP 1: A thorough understanding of the component production process. This step is crucial to draw conclusions about subsequent quality, logistics and construction requirements.
- WP 1.1: This work package provides the basis for further analysis in WP 2 and 3. All relevant parameters of AM techniques and corresponding key performance indicators concerning the component scale that may have an impact on the production, logistics and construction processes are identified.
- WP 1.2: The central objectives are to develop efficient methods for a reliable acquisition of actual component geometries and comparison of capturing output with the respective digital model.
- WP 1.3: develops methods for a reliable detection of defects in additively manufactured building components and investigate techniques for iterative quality improvement.
- WP 1.3.1: deploys Machine Learning techniques for defect classification that may occur during the printing process.
- WP 1.3.2: Iterative improvement of the surface will be developed based on the defect detection from WP 1.3.1.
WP 2: Dedicated on the building scale. Investigation on strategies for the important step of assembly that are embedded in a model of the entire production process. Considering surveying methods in order to establish feedback loops to the BIM model.
- WP 2.1: Investigates on the integration of AM into the production chain and data exchange.
- WP 2.2: Investigation on creating a bi-directional workflow bridges between the BIM model and the construction site.
- WP 2.2.1:Creation of a common coordinate system between BIM and on-site. Also, robot-positioning interface will be investigated.
- WP 2.2.2: Usage of mixed reality for in-site assembly for efficiency increasing, accuracy and error reduction.
- WP 2.3: Strategies development to build a relationship between the as-built and as-modelled of the components and building.
WP 3: A development of a holistic view to demonstrate the impact of additive manufacturing on project delivery systems in the construction industry.
- WP 3.1: Analyzation of new working procedures and tasks in project delivery system may be affected by new methods implementation. Furthermore, how the traditional organizational setup needs to be adapted in order to maximize the benefit of AM.
- WP 3.2: Questions on the emergence of new roles for people within the process chain and the role of new business models for companies.
Networking with other projects
Due to the integration of additive manufacturing in the construction process, this project plays a key role throughout the TRR. To be able to examine three different scales of additive manufacturing, links to various projects are necessary:
- A01, A02, A03, A04 and A05 for integrating AM methods
- B04 and B05 for integrating the AM process control
- C02, C04, C05 and C07 for integrating design and construction methods.