Research Summary Report of B05
Principles of Mobile Robotics for Additive Manufacturing in Construction
[21.10.2022]
Dielemans, Gido; Doctoral researcher, gido.dielemans@tum.de,
Technical University of Munich, Department of Architecture, TT Professorship Digital Fabrication
This research examines the architectural implications of mobile robotics for AM in construction and develops methods for their implementation. The material deposition method of clay and concrete extrusion 3D printing is used to investigate mobile part-based AM strategies, that is, to produce large objects whose size exceeds the static workspace of the robot. By implementing advanced sensor and control solutions, autonomous localization and precise manipulation techniques for mobile AM are explored. In addition, this research aims to provide scalability to AM processes by examining the use of multiple robots to collaborate on single fabrication jobs. The objective of this research is to develop mobile AM technology for its direct implementation on construction sites.
Summary
By using a mobile platform for AM, it is possible to produce objects larger than the system’s static workspace by using the dynamic workspace. However, using the dynamic workspace introduces uncertainties into the process, since operation is under conditions of limited prior knowledge. In a first step, this is addressed by using the robots in quasi-stationary mode, i.e., the mobile platforms are navigated to a defined location to carry out a 3D printing task stationary. The static working area of the mobile robots is thereby calibrated in relation to the position where the object is to be manufactured.
To experimentally investigate the fundamentals of part-based fabrication with mobile robots, a bespoke column formwork was printed of individual segments by a single mobile platform performing clay extrusion from 51 different locations around a reinforcement cage. This formwork was then gradually filled to mitigate the amount of pressure being applied to the printed structure, while providing shape stability to the clay segments that allows for the additive manufacturing process to be carried out with this slow-hardening material (Fig. 1 and Fig. 2).
Current state of research
In the case study “Clay Formwork”, a two-tiered sensing strategy was adopted in collaboration with B04, where coarse localization is performed with a 2D SLAM algorithm, which estimates the robot’s location in a global map with ±60mm precision. After this coarse localization, a scanning routine is performed on the previously printed workpiece to estimate the location of the mobile platform in relation to it with the required precision for printing, that is, in the range of ±2mm. For this purpose, two point clouds are fitted to one another, a scan of the work piece that is recorded from the original position of the robot , and a point cloud that is recorded after the robot is relocated. The transformation resulting from this fitting procedure corresponds to the transformation from one robot location to another. However, during these studies, a discrepancy between scales of accuracy has been noted, which requires further investigation. Thus, for the full-scale study of printing the formwork, an additional localization approach was used, in which reference points where probed with human aid, allowing for estimation of the platform’s location with the required precision of ±2mm.
The bespoke concrete column was finally constructed by the additive manufacturing of 51 clay segments, from the respective amount of fabrication locations, around a reinforcement cage. The geometry of each segment was adjusted to follow the curvature of the column and appended with an increased contact patch at the edges, as well as a set of stiffening fins, for the clay formwork to better withstand the hydrostatic filling pressure. Each time a set of three segments is completed, a new filling of concrete is added, which fixates the geometry of the column and provides rigidity to the clay segments. A lightweight concrete was used to reduce the hydrostatic pressure on the formwork and to decrease the final weight of the structure. The mixture was finely adjusted to achieve a high form-filling capacity with a fast thixotropic response. This allows for the continuation of the additive manufacturing process, without requiring the formwork to harden. When the last segment was constructed and the concrete had set, the segments could be removed, revealing the final reinforced concrete structure (Fig. 3/4 and Fig. 5).

Figure 1: Experimental setup for part-based AM of a clay formwork for a reinforced lightweight concrete column.
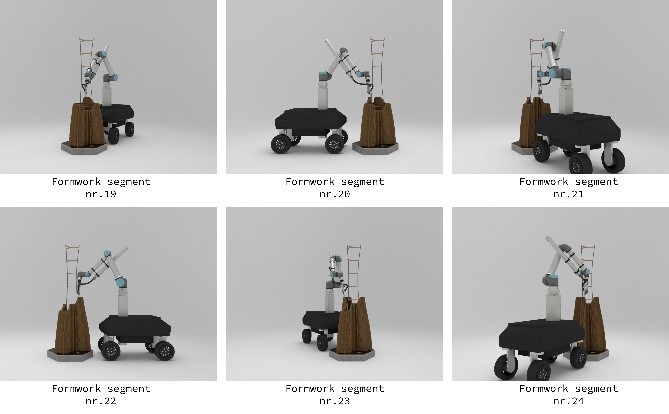
Fig. 2: Succession of six locations for the manufacture of six segments around the rebar cage, followed by another cycle of filling the formwork.

Fig. 3: Fabrication of the bespoke reinforced concrete column by means of a segmented reusable clay formwork.

Fig. 4: Fabrication of the bespoke reinforced concrete column by means of a segmented reusable clay formwork.
Fabrication of a bespoke reinforced concrete column, by means of a segmented reusable clay formwork for part-based mobile AM.