Research Summary Report A07
Wire and Arc Additive Manufacturing (WAAM) of complex individualized steel components
[22.04.2022]
Müller, Christoph; doctoral researcher,
TU Braunschweig, Institute for Structural Design (ITE)
The aim of TP A07 is the design, the manufacturing and the testing of complex individualized steel components by means of WAAM. That contains the fundamental investigation of design and the design process for WAAM components. For the manufacturing of steel components by WAAM, stable and reliable processes for basic geometries are qualified and based on that, case study demonstrators for the identification of manufacturing restrains are fabricated. Furthermore a novel approach for material and component testing is developed to identify local material and component properties.
Summary
In the regularly published literature on additive manufacturing, the fabrication processes are impressively demonstrated on geometries. The generation and considerations behind the creation of the geometries is usually not the subject of the reports. Often, these geometries are created manually by the authors of the reports with the knowledge of the process limits. Another variant is to use the processed output of a topology optimization by means of FEA software. Here it is possible to take into account the limits that each manufacturing process imposes on the geometry. A typical constraint encountered in most processes is the overhang of material with respect to the build direction. It is therefore of great interest to take this into account in the design process of the force flow optimized geometry. As the number of constraints from the manufacturing process increases, so does the effort required to create the geometry to be manufactured.
The approach of the working group Kloft in the subproject A07 of the AMC is the geometry generation by means of self-organizing systems. The goal is to generate geometry while taking into account several constraints from additive manufacturing process.
Current state of research
Since the last report, the basic mechanism for force flow optimization has been modified. As before, the problem of optimizing a volumetric geometry is approached by discretizing it as a space truss. The nodes within the truss serve as agents and are moved in an iterative process. The difference to the previous approach is the decision making of the points, which direction of movement they will take. A classical greedy heuristic is now applied here and the network serves as a graph of the problem. This leads to a smoother geometry with less errors. The improved basic geometry from the force flow optimization is necessary to be able to consider boundary conditions from the fabrication process.
The first geometric boundary condition that was implemented was the minimum wall thickness of the geometry. This is because the geometry should not be thinner than the width of the weld seam at any point. These boundary conditions depend exclusively on the surface mesh of the geometry. The minimum thickness is controlled by the distance between opposing faces. (Fig. 2) Only with a consistent alignment of all normal vectors of the surface of the mesh was it possible to implement this boundary condition.
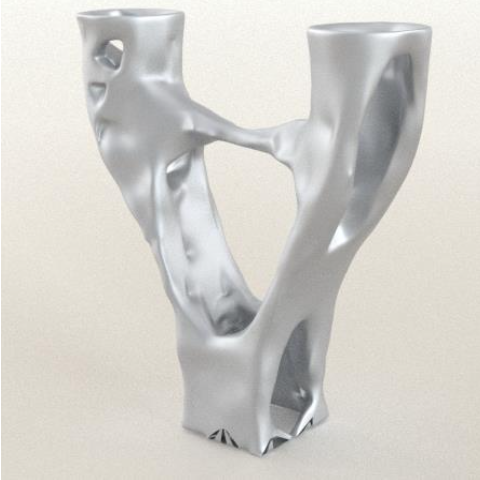
Fig 1: Rendered node created using the presented method. The first boundary condition of the minimum wall thickness was implemented at each point. Credit: ITE, TU-Braunschweig

Fig 2: Schematic representation of the rule for maintaining the minimum thickness. The decisive factor is the distance from the point under consideration to the intersection of the surface with the rays. / Credit: ITE TU-Braunschweig