Research Summary Report B04
Process Control and Adaptive Path Planning for Additive Manufacturing Processes Based on Industrial Robots with an Extended Degree of Freedom
[19.08.2022]
Lachmayer, Lukas; Doctoral researcher, lachmayer@match.uni-hannover.de
Leibniz Universität Hannover, Institute of Assembly Technology (match)
Function integration, topology optimization and automation increase productivity through the reduced workload, sustainability by less applied material and safety by decreasing manual labour. These benefits are condensed in most additive manufacturing processes, and thus, these are of significant interest to the construction industry. However, the time- and environment-dependent material properties of fresh concrete reduce the predictability of the material and thus often lead to component collapses during the manufacturing process. This project aims to achieve repeatability within concrete-based robot-guided additive manufacturing processes.
Summary
As expected and shown in Fig. 1, repeatability experiments using the shotcrete 3D printing process (SC3DP) result in severe height and width deviation. While SC3DP is a destabilizing process and particularly hard to control, similar discrepancies between as-planned and as-printed geometry can also be observed for extrusion processes or even wire-and-arc additive manufacturing. Within the framework of the research project B04, a multi-model based printing-method is utilized to increase the repeatability of SC3DP and achieve a print-as-planned geometry. This method first applies an empirical strand-geometry model to the designed CAD file to generate a continuous printing path. This path is transformed into a FEM simulation to evaluate the risk of elastic buckling and plastic collapse. Based on the simulation results, the print speed is adjusted, and if necessary additional inter-layer waiting times are added to ensure stability. During the printing process, the applied strand geometry and overall component dimensions are surveilled by the online-process-control unit shown in Fig. 2. The strand data is transferred into controller values by applying a strand-correction model. The correction model is based on feed-rate and spray-distance experiments. Connecting a priori path geometry prediction, the FEM-based path optimization approach and the online geometry control enabled us to print three wall structures of 2 meters of height within a repeatability window of +/- 2.6 mm. The walls shown in Fig. 3 were produced in close cooperation with project A04.
Current state of research
Since the overall multi-model-based approach proved advantageous in the 2.5D printing process, we now aim to apply the methods to 3D printing operations. Therefore we are currently developing algorithms to calculate the controller set-points based on 3D print paths. Whilst the positioning of the 2D scanner is reasonably easy to solve, we have to consider the offset between the scanner and material application to get to height and width values within the field of view of the scanner. Furthermore, additional ways to feed back the FEM modelling results into the generated print path, either on material properties adjustment or with structural component optimization, are investigated.
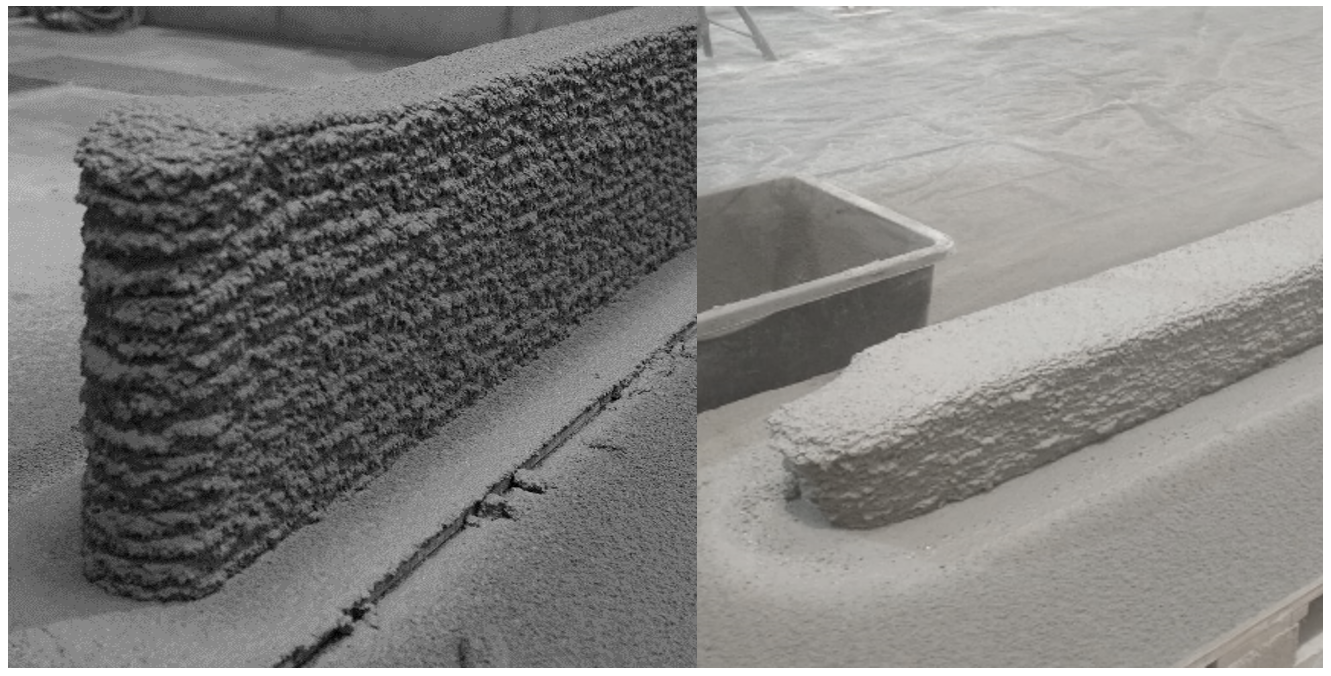
Fig 1: Wall segment repetition, printed with identical parameters, same system and unchanged material settings. The height and width deviation is at about 50% / Credit: match, ITE