Research Summary Report of A04
Integrated Additive Manufacturing Processes for Reinforced Shotcrete 3D Printing (SC3DP) Elements with Precise Surface Quality
[11.04.2025]
M. Sc. Jennifer Rudolph Researcher, j.rudolph@ibmb.tu-bs.de
TU Braunschweig, Institute of Building Materials and Concrete Construction and Fire Safety (iBMB)
M. Sc. David Böhler Researcher, david.boehler@tum.de
Prof. Dr.-Ing. Dirk Lowke Project leader, lowke@tum.de
TU Munich, Department of Materials Engineering
Project A04 investigates cooperative Additive Manufacturing (AM) processes based on Shotcrete 3D Printing (SC3DP). The aim of this project is to fundamentally understand the SC3DP technology to manufacture sustainable, multi-objective optimised, reinforced concrete components with geometrically precise surface quality and improved building physics by functional integration.
Current state of research
The following two papers are the result of research conducted under the A04 project and have been published as part of Digital Concrete 2024. They demonstrate the recent developments of our research.
Durability of 3D Printed Concrete: A Comparison of Extrusion 3D Printing, Shotcrete 3D Printing and Conventional Casting[1]
The advent of 3D concrete printing technology in the construction industry has led to an increased focus on the durability of 3D printed concrete. Traditionally, cast concrete has been considered to be largely homogeneous. However, the layer-by-layer manufacturing process of 3D concrete printing can result in microstructural differences that affect resistance to environmental impacts.
This paper compares two common 3D printing methods, Extrusion 3D Printing and Shotcrete 3D Printing (SC3DP with 0% and SC3DP_3 with 3 % accelerator), with conventionally produced concrete (cast). The focus is on how well these different types of manufacturing methods withstand potentially harmful environmental influences, particularly carbonation caused by CO₂ and chloride penetration, which plays a key role in the corrosion of steel reinforcements. In addition, it was investigated how the penetration fronts vary depending on the manufacturing process.
The findings show differences between the fabrication methods: SC3DP samples exhibited greater resistance to chloride penetration, but their resistance to CO₂ was lower, meaning they carbonated more quickly than extruded or conventionally cast samples. Furthermore, the 3D printed concretes showed uneven penetration fronts, with weak points in different areas: While the extruded samples showed the highest penetration depth in the bulk zone, the SC3DP samples (especially with accelerator dosage of 3% (SC3DP_3)) showed the highest penetration depth in the interface zone (see Figure 1). Depending on the 3D printing method, distinct penetration front profiles emerged: a sawtooth-like profile for the SC3DP process and a wave-like profile for extrusion (see Figure 1).
These findings underline that the durability of 3D-printed concrete depends not only on the layered manufacturing process itself but also on process-specific factors such as pumping or spraying the concrete. Research in this area is still essential to further establish 3D printed concrete as a viable alternative to conventional construction methods.
Design and Characterisation of a Two-Component Mortar System for Shotcrete 3D Printing: An Approach to the Targeted Control of Material Properties[2]
Shotcrete 3D Printing is an innovative additive manufacturing process that enables the rapid, formwork-free production of large-scale concrete structures. However, ensuring the structural integrity of printed elements requires an optimised balance between material workability and early-age strength. A key challenge in SC3DP is achieving sufficient flowability for pumping while simultaneously enabling rapid stiffening to support overlying layers.
In order to address this challenge, a novel two-component mortar system has been developed recently2. The system consists of two separately mixed, retarded mortars – one based on calcium sulfoaluminate cement (CSA) and the other on a Portland cement-metakaolin-limestone blend (CC). When combined at the nozzle, the mortars undergo an accelerated reaction, providing precise control over rheological properties and early structural build-up. Experimental investigations, including calorimetry, penetration testing, and mechanical strength analysis, demonstrated that the reaction kinetics and structural build-up could be tailored by adjusting the mixing ratio of CSA and CC mortars. Different mixing ratios in the 2-component system allow the rheological properties to be modified. A higher proportion of CC mortar results in faster initial structural build-up, whereas a higher proportion of CSA mortar leads to slower initial yield stress evolution but very high early strengths within the first few hours (see Fig. 2).
[1] Böhler, D., Mai, I., Lowke, D. (2024). Durability of 3D Printed Concrete: A Comparison of Extrusion 3D Printing, Shotcrete 3D Printing and Conventional Casting. In: Lowke, D., Freund, N., Böhler, D., Herding, F. (eds) Fourth RILEM International Conference on Concrete and Digital Fabrication. DC 2024. RILEM Bookseries, vol 53. Springer, Cham. https://doi.org/10.1007/978-3-031-70031-6_33
[2] Rudolph, J. V., Lowke, D. (2024). Design and Characterisation of a Two-Component Mortar System for Shotcrete 3D Printing: An Approach to the Targeted Control of Material Properties. In: Fourth RILEM International Conference on Concrete and Digital Fabrication. DC 2024. RILEM Bookseries, vol 53. Springer, Cham. https://doi.org/10.1007/978-3-031-70031-6_26
How durable is 3D printed concrete compared to traditional casting? Our latest results show that the manufacturing method plays a key role in how well concrete resists environmental influences. While cast concrete is known for its relatively uniform structure, 3D printed concrete shows more variation internally — and this affects durability. In our tests, 3D printed samples exhibited greater resistance to chloride penetration in some cases, but also showed faster carbonation and less uniform penetration fronts. The image illustrates chloride ingress across different samples — from conventionally cast concrete on the left to 3D printed concrete on the right. These findings highlight the importance of understanding how the layered printing process influences long-term performance.
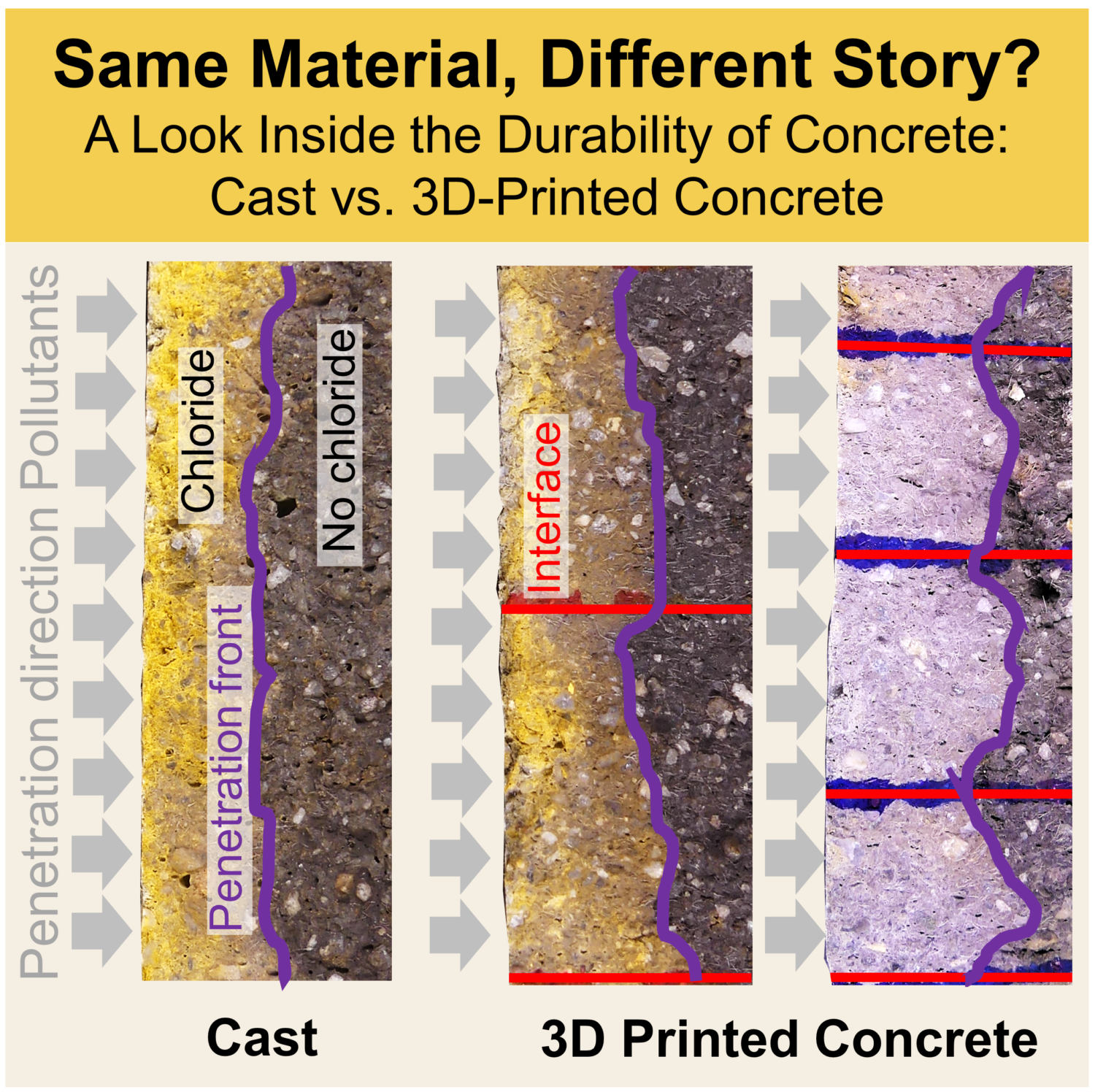
Fig 1: Penetration behaviour over cross-section height (a) chloride migration and (b) carbonation. Penetration of pollutants into the concrete from left to right. Credit: Böhler et al. (2024)1
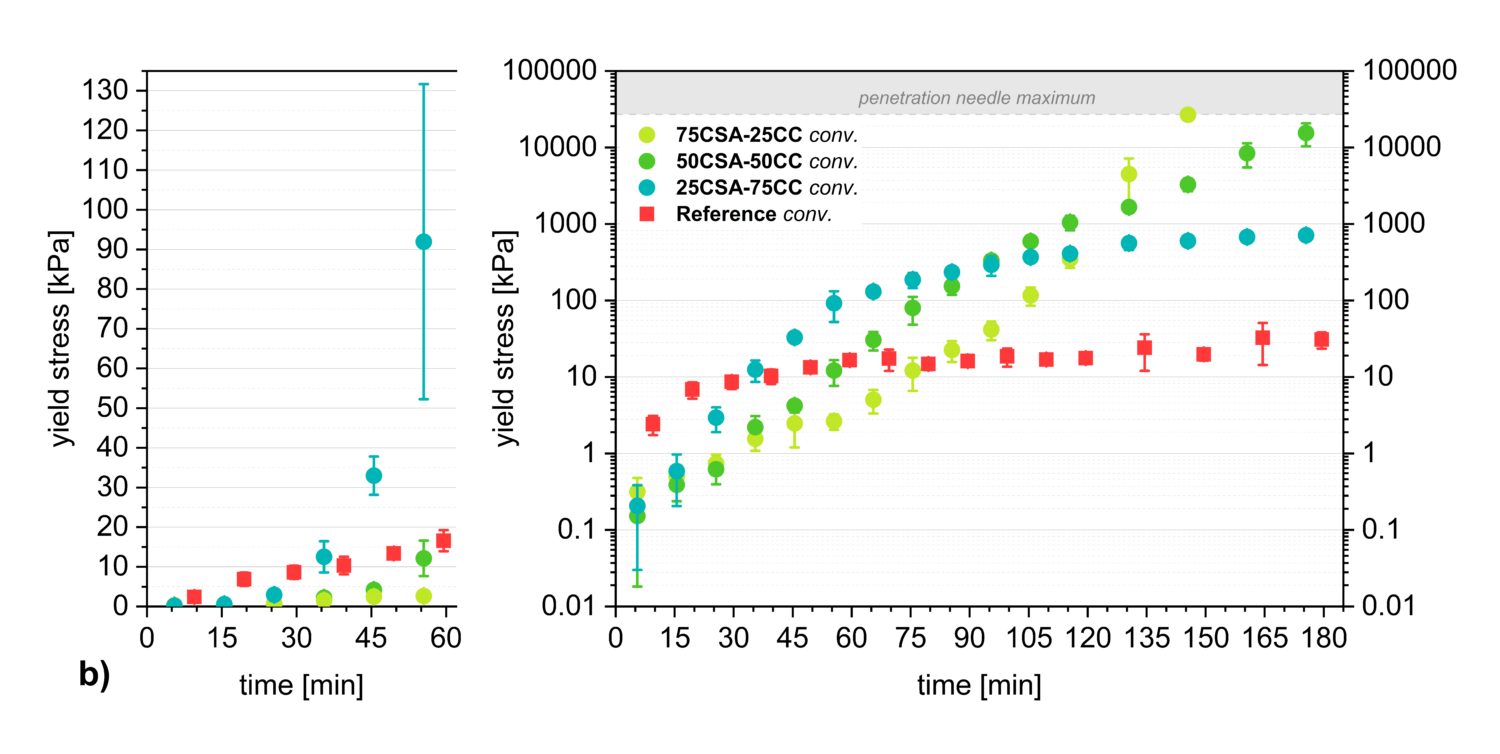
Fig 2: Yield stress evolution over 180 minutes for the 2K-System in varied mixing ratios, compared to the reference mortar.; Credit: Rudolph et al. (2024)2